TIME
As C.F.Martin & Co approaches the rare honor of commemorating the 2,000,000th recorded serialized instrument, we sought to create a tribute that acknowledges the unprecedented contribution to the craft of lutherie and to celebrate the generations who've known Martin as the benchmark for tone. "Time". . . we're always chasing it. . .there's never enough of it. . .and music requires its' precision. A team comprised of Martin's CustomShop, Instrument Design, Engineering and other disciplines collaborated with artist Robert Goetzl, industry materials partners, and exclusively with RGM Watches- also a family-owned Pennsylvania company. As guitar enthusiasts, we came to realize that our passions aren't limited just to the guitar. Rather, our appreciation extends to other areas of our lives where the presence of quality, design commitment, and precision are also at play. Like many of the customers in our extended family, we also love good watches. How better to mark the passing of time since our modest appearance in 1833 than by combining traditional acoustic elements, leading edge construction & inlay concepts, and a masterpiece of timekeeping form.
This gallery offers a collection of key moments spanning the concept, collaboration, and construction of our museum-owned Serial # 2,000,000.
we're always combing through watch mags. we often find ourselves inquiring on the wristpieces of guests to the Custom Shop.
Robert Goetzl brainstorms the inclusion of special components and materials across the guitar platform.
first round of artistic drafts to assist further collaboration with an expanding group of partners.
RGM watches begin consulting on the scope of project and our desire to incorporate elements of time into our "Passing of Time" project.
Inspection of RGM's chassis samples show a level of manufacturing detail that can scramble the mind.
Finished examples of RGM's bespoke movement are art in motion- pure and simple.
C.F. Martin IV is a long-time fan of quality watches, so he takes a personal interest in the concept of the project and the relationship with our partners.
Roland Murphy of RGM Watches explains how our quest to incorporate credible elements of watch building into a platform this large will present special challenges for the design and build teams.
The goal of utilizing accurate movement elements AND true positioning is established.
Roland inspecting placement renderings for a one-of-a-kind movement and housing to be mounted within the head stock.
Placement considerations for actual movement pieces on an ebony fret board.
Creating a hybrid mechanical movement from a proven power train.
Robert and Roland laying out visual concepts to recreate in true mechanical parts.
Digital modeling has required countless hours to create a standalone timepiece.
Calculations, calculations, calculations. Measure often because we only hope to cut once.
Individual components from a working timepiece are evaluated for layering into a guitar using emerging new techniques.
Relationships between components are relentlessly checked prior to final modelling.
The project will apply elements of mechanical movement not only into the guitar, but also with proper mechanical position.
Continued modelling shows the concept of building a watch "through" the guitar. The pieces on top relate top down through the gear train of a working timepiece.
Modeling of the head stock to accommodate a working timepiece and specially manufactured tuning machines to achieve material singularity for the case and crown-theme tuners.
Tuning machine rendering.
Test production on movement components.
Test production on movement chassis components.
Collaborating on whether or not to include gold winding crown caps on the tuning machines.
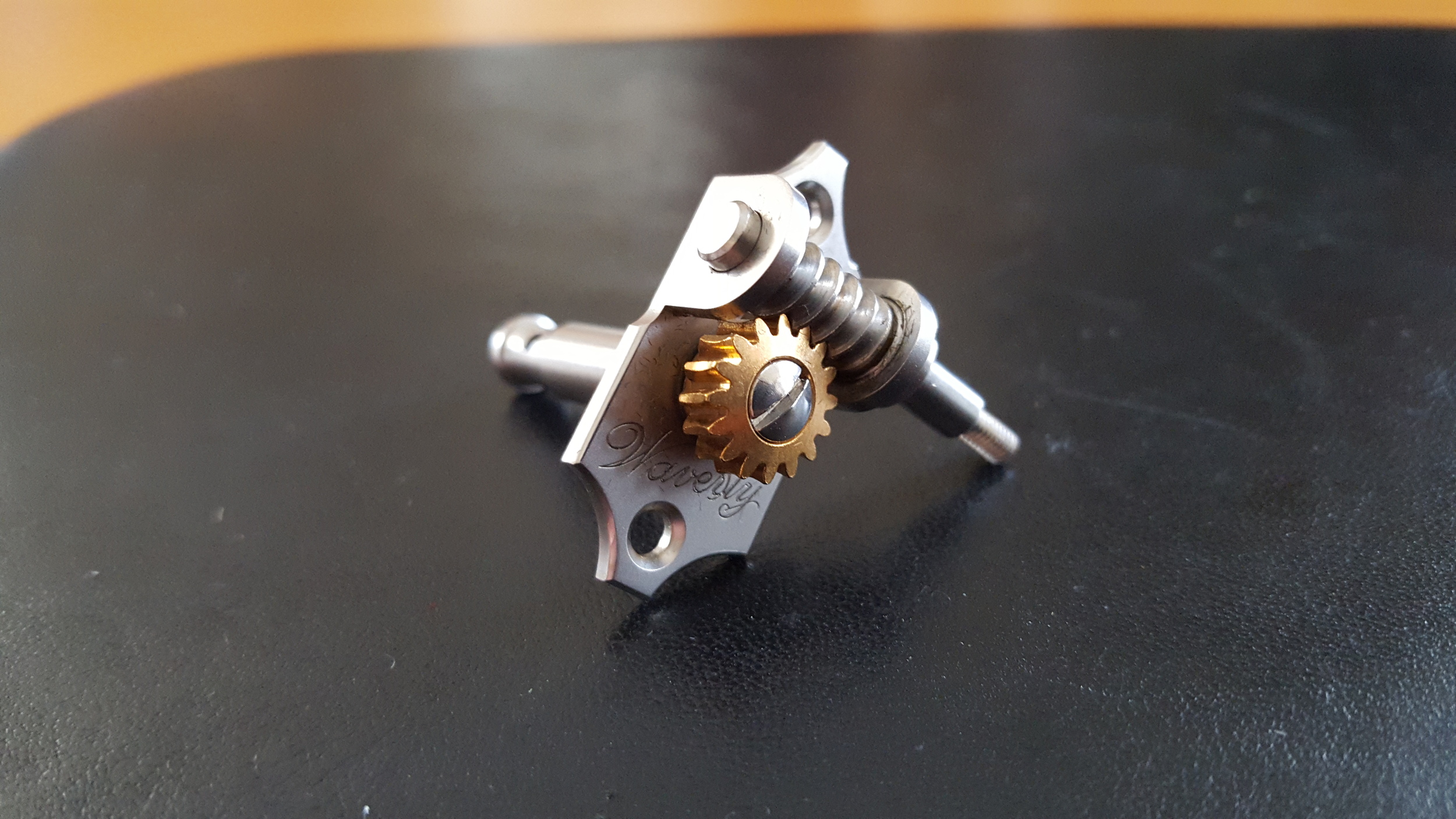
Custom manufactured vintage style tuning machines.
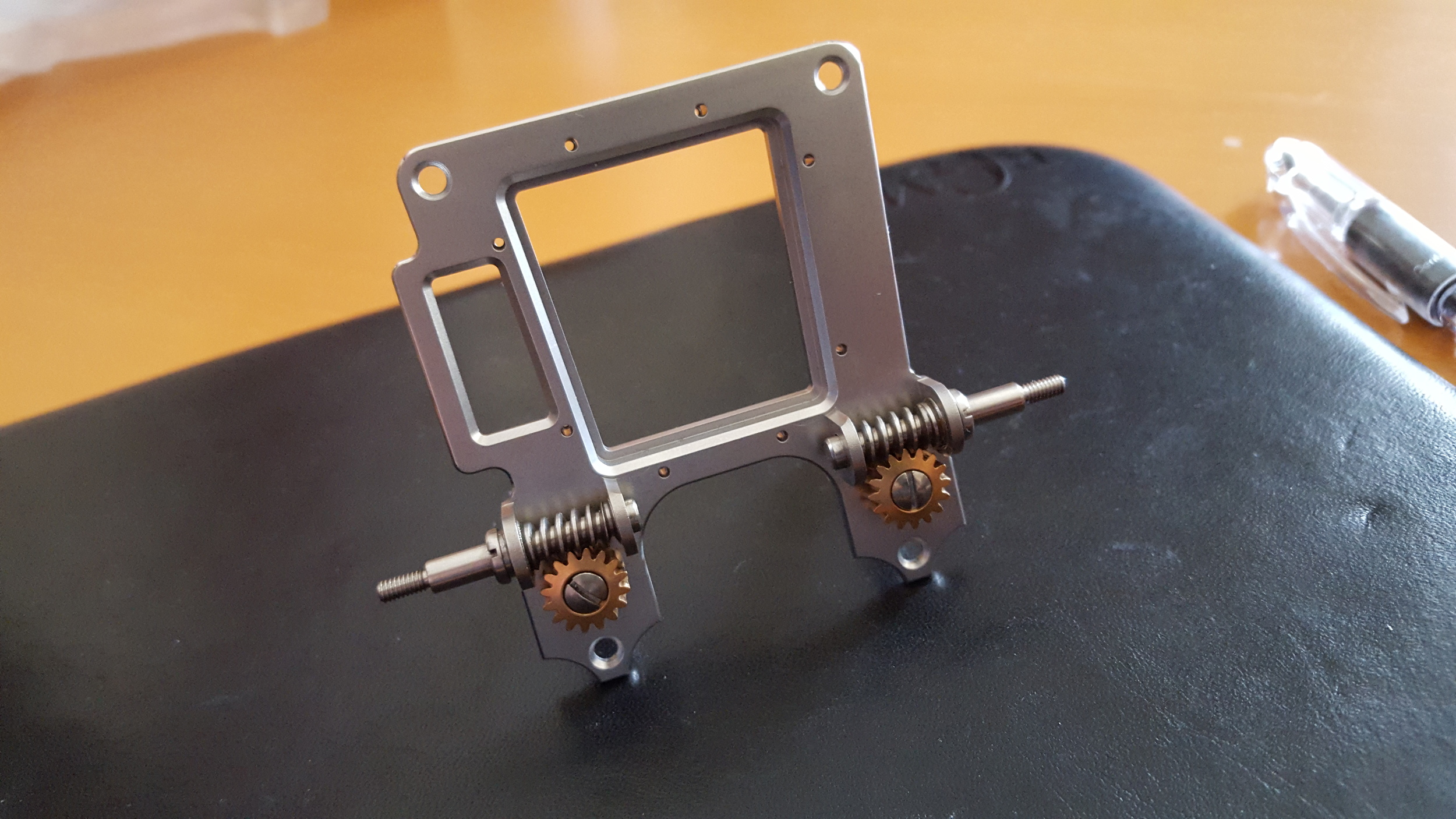
World's first purpose built watch case designed to follow the iconic C.F. Martin head stock profile.
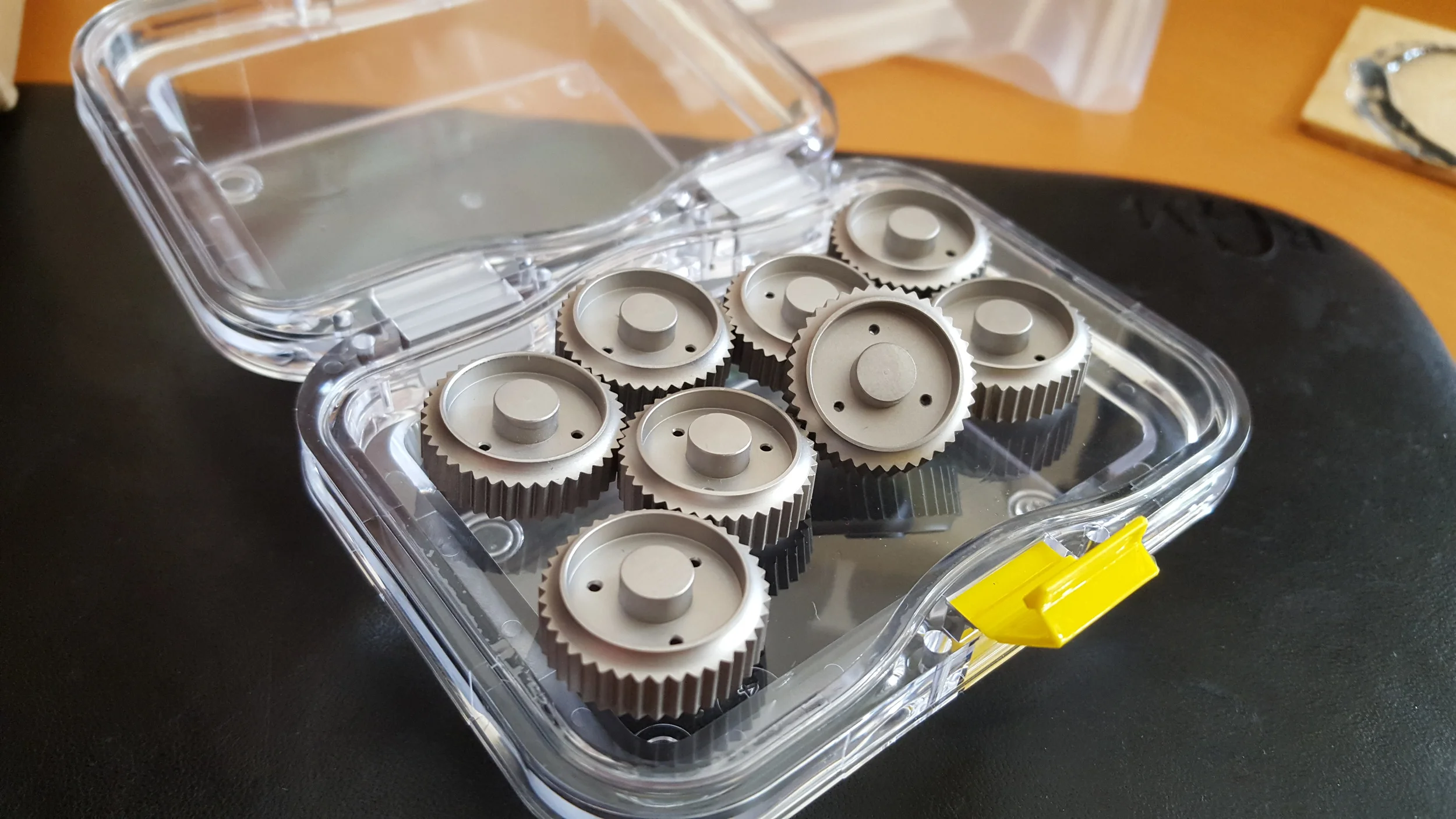
Custom cut tuning knobs that mimic the feel of a winding stem. . . in jumbo form.
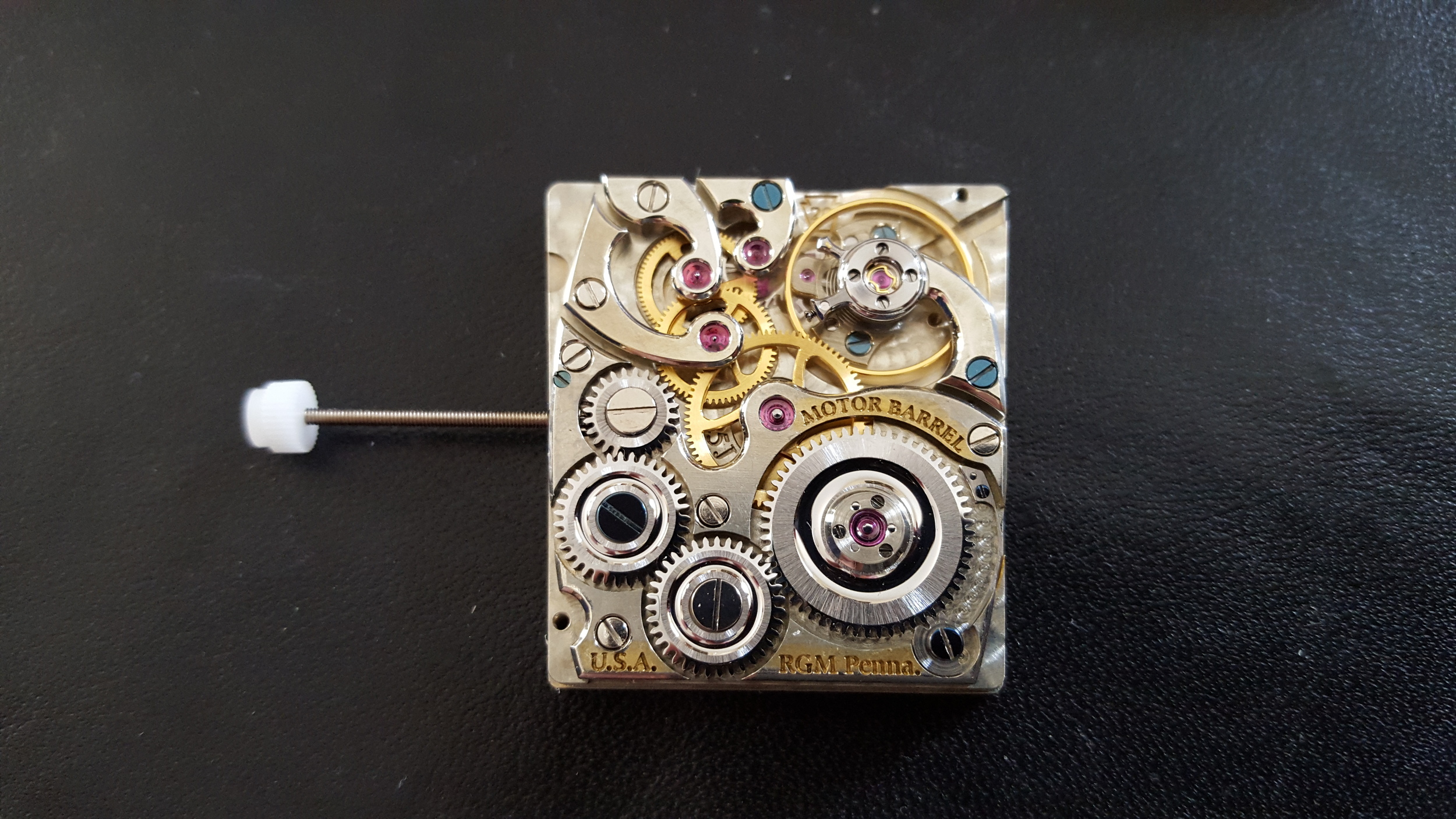
Actual watch movement from test production ready for extreme scrutiny, quality evaluation, and additional dressing of components.
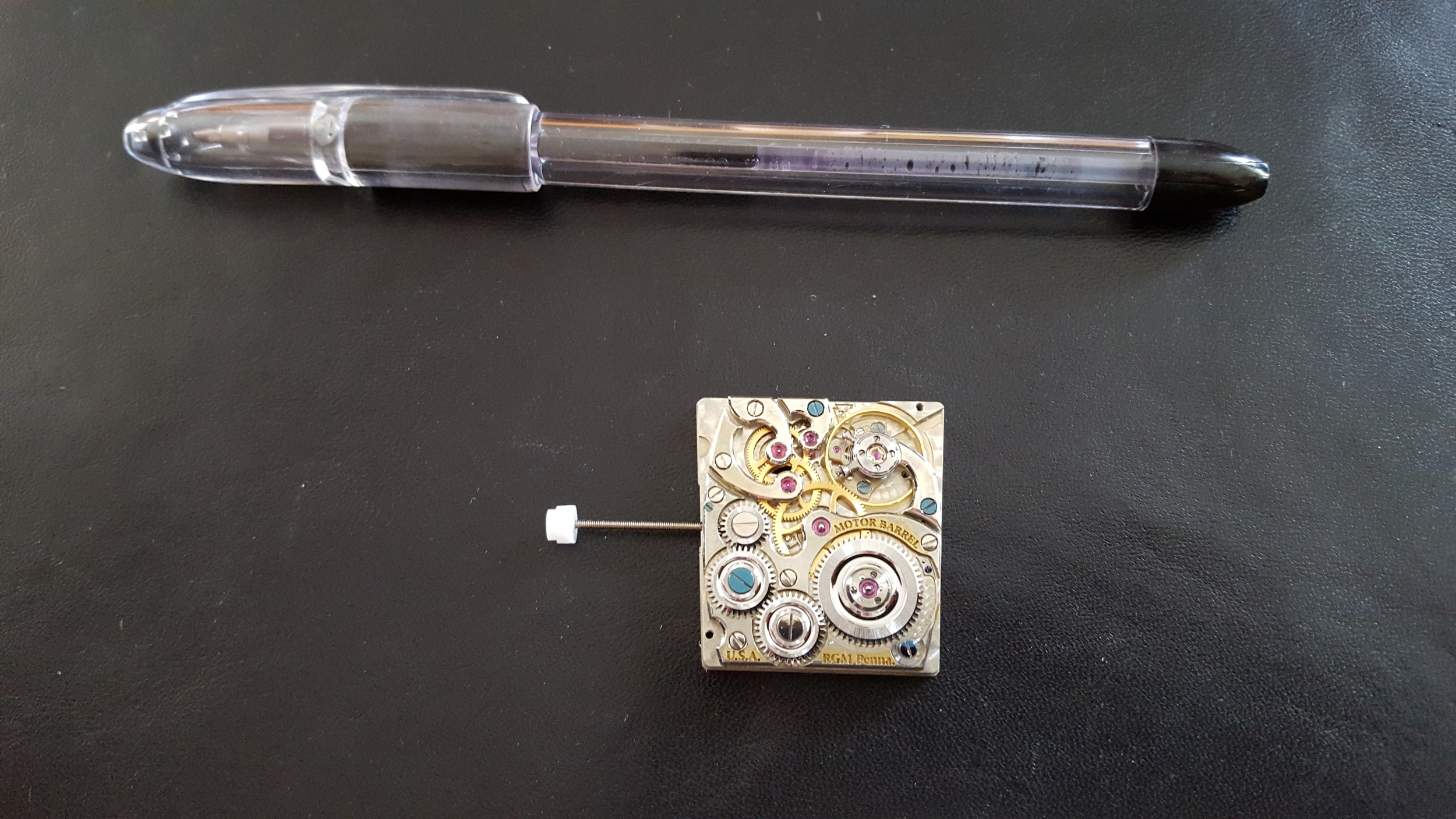
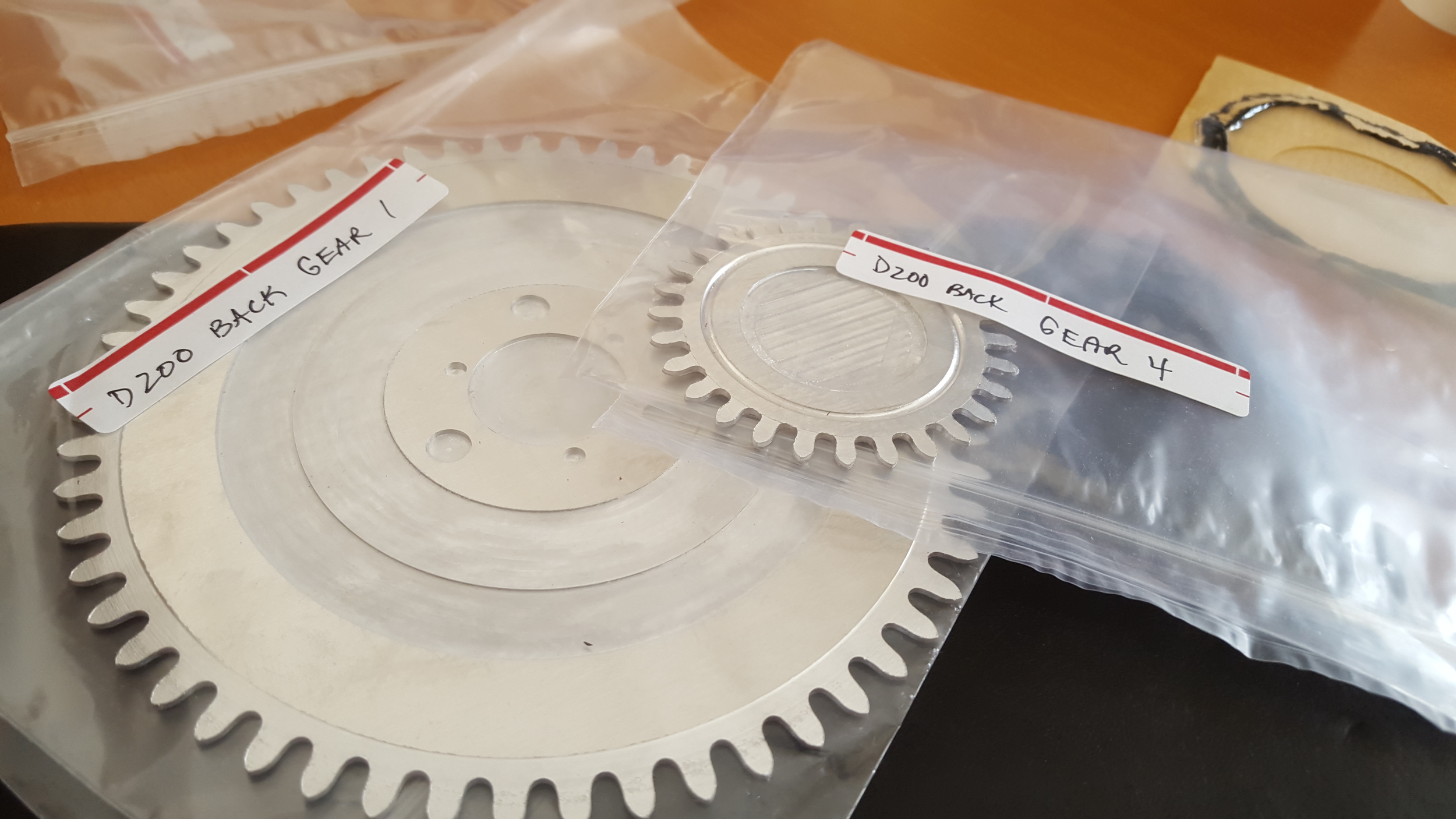
Large format pieces for guitar inlay being readied for embellishment by Roland Murphy and his team of master technicians.
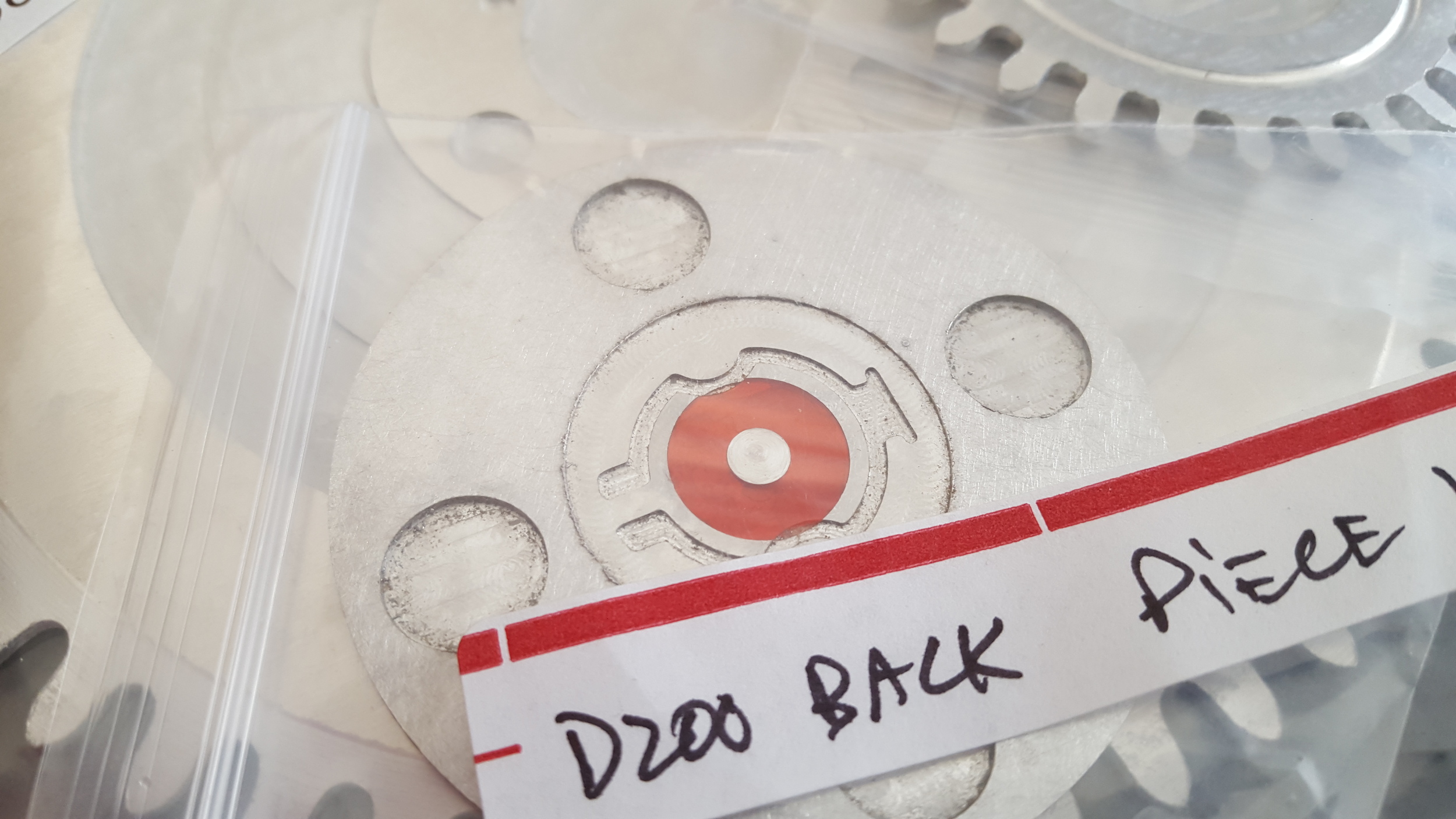
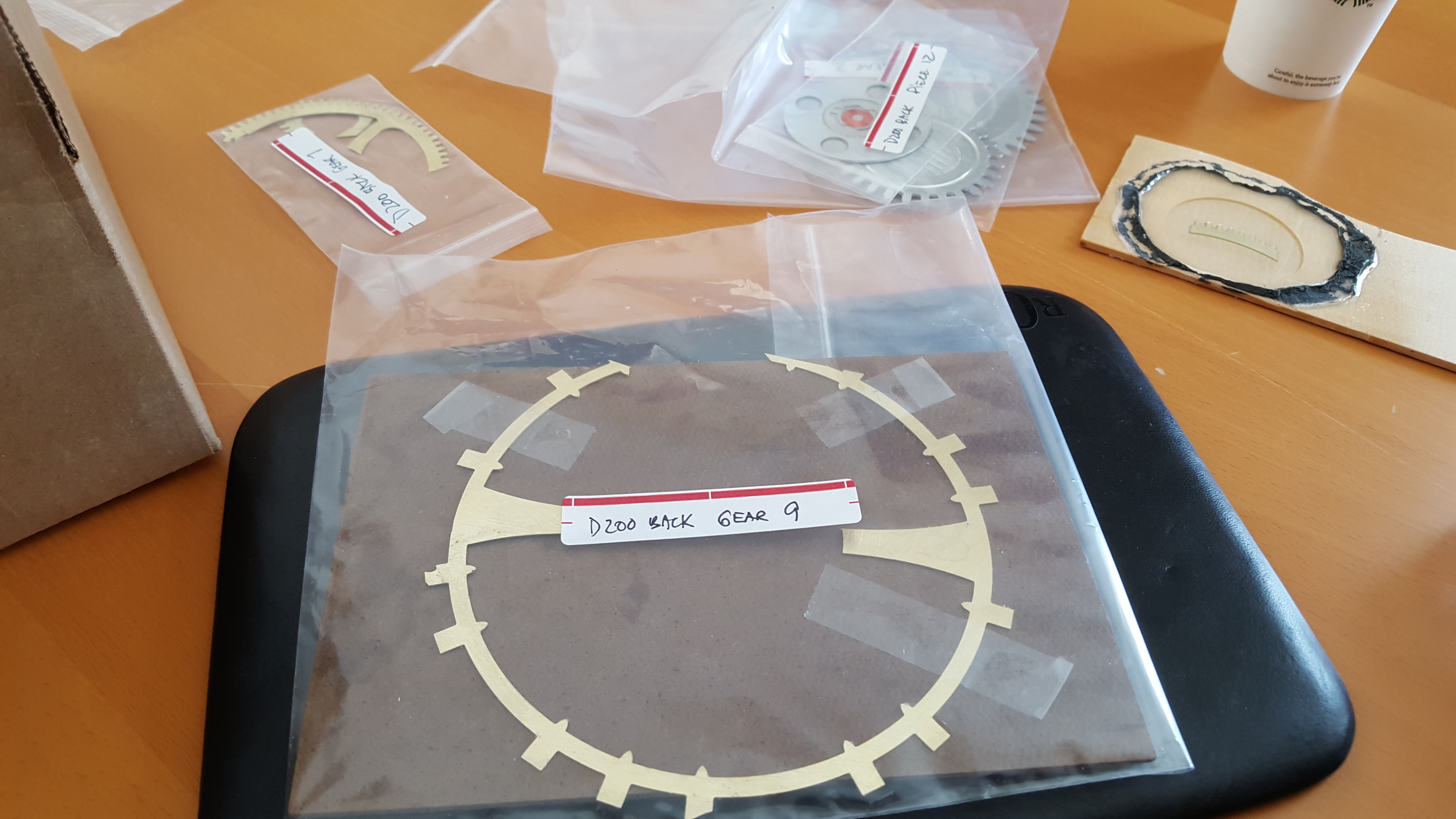
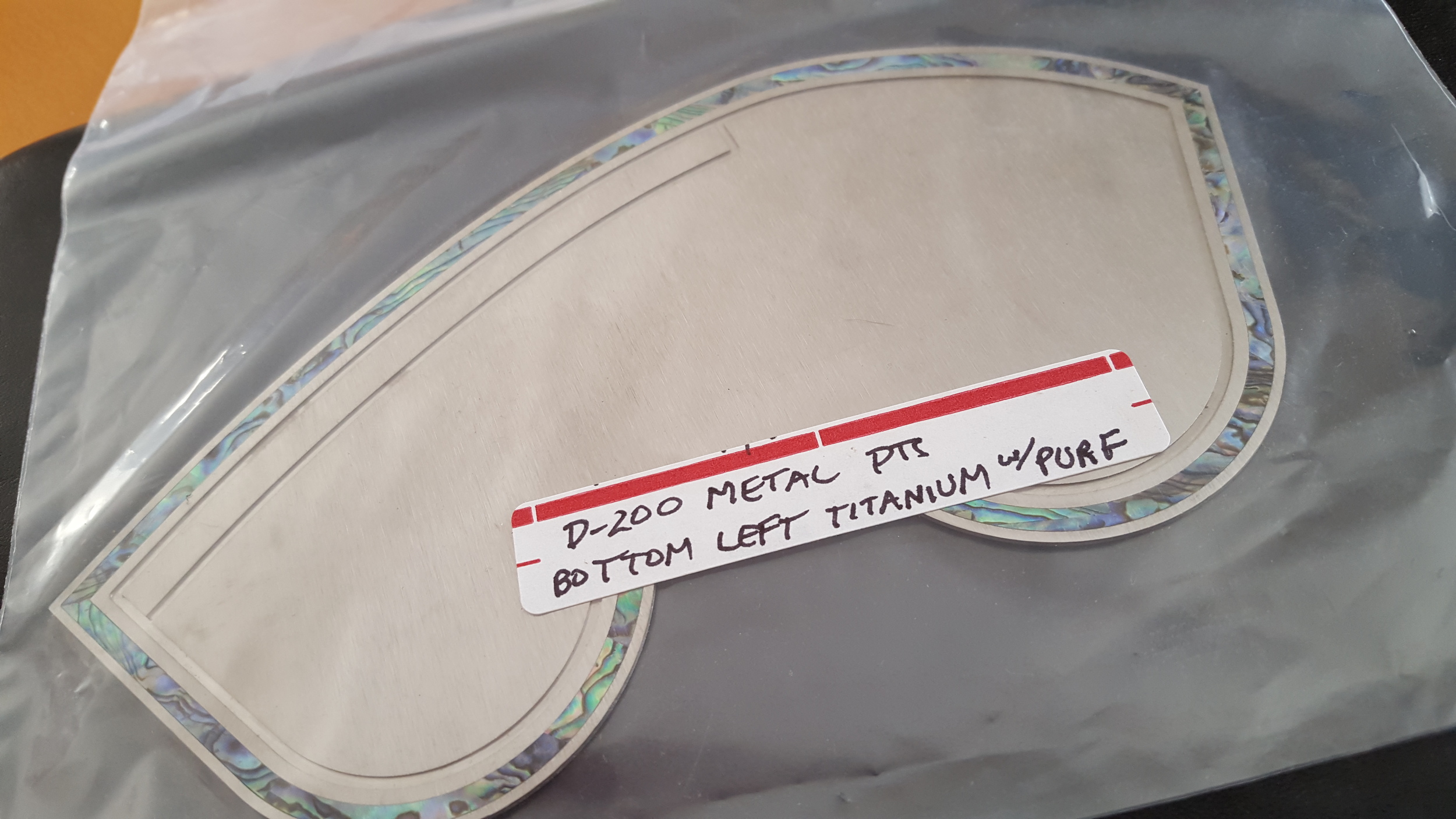
One of the many ancient machines employed by RGM Watches to create the unique appointments found among the guitar inlay pieces and the watch movement.
This clutch-looking contraption is called the rosette, and it's used to perform the painstaking task of applying Guillochè.
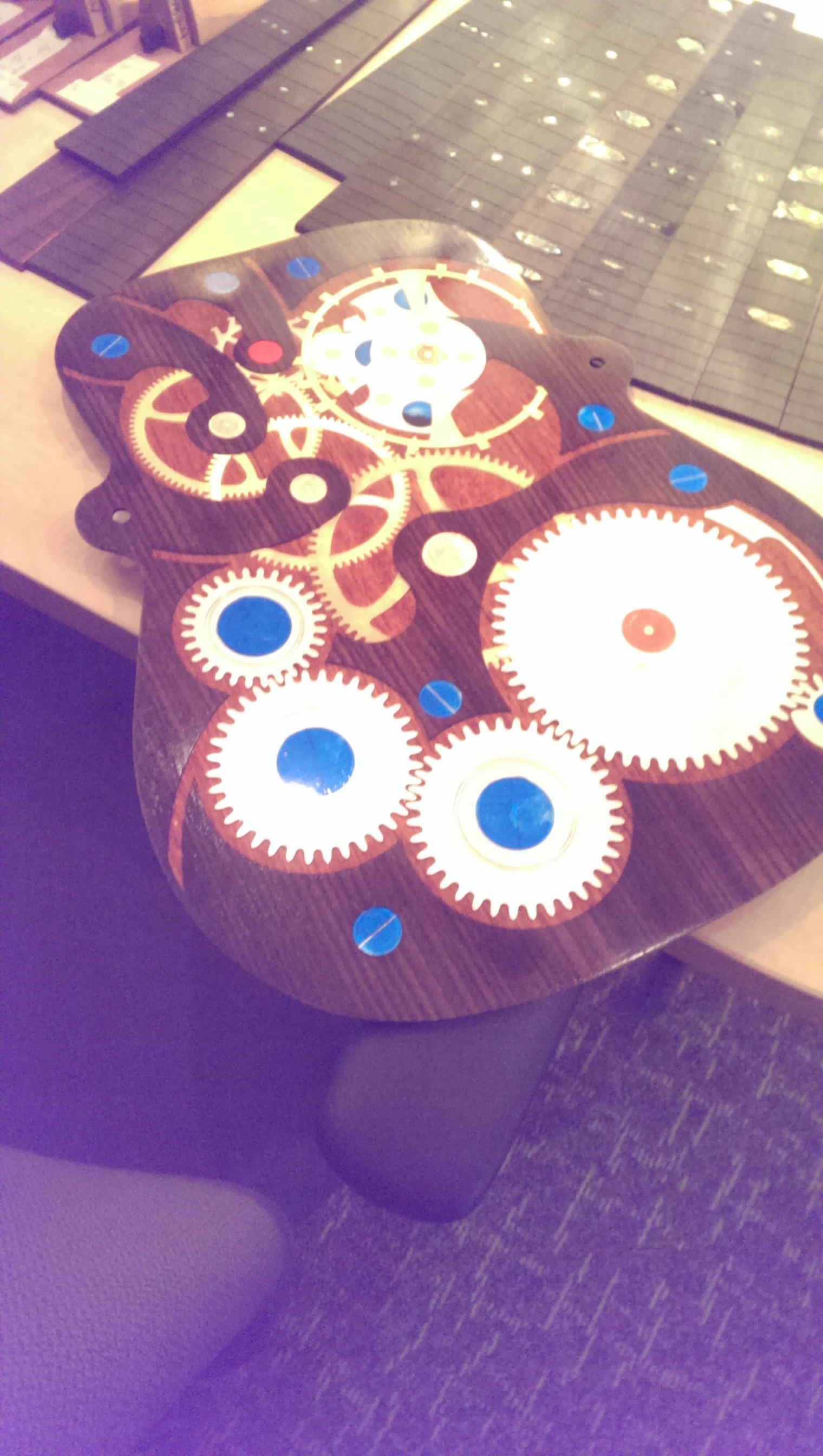
Test application of inlay components into a rosewood back. Prototype phase.
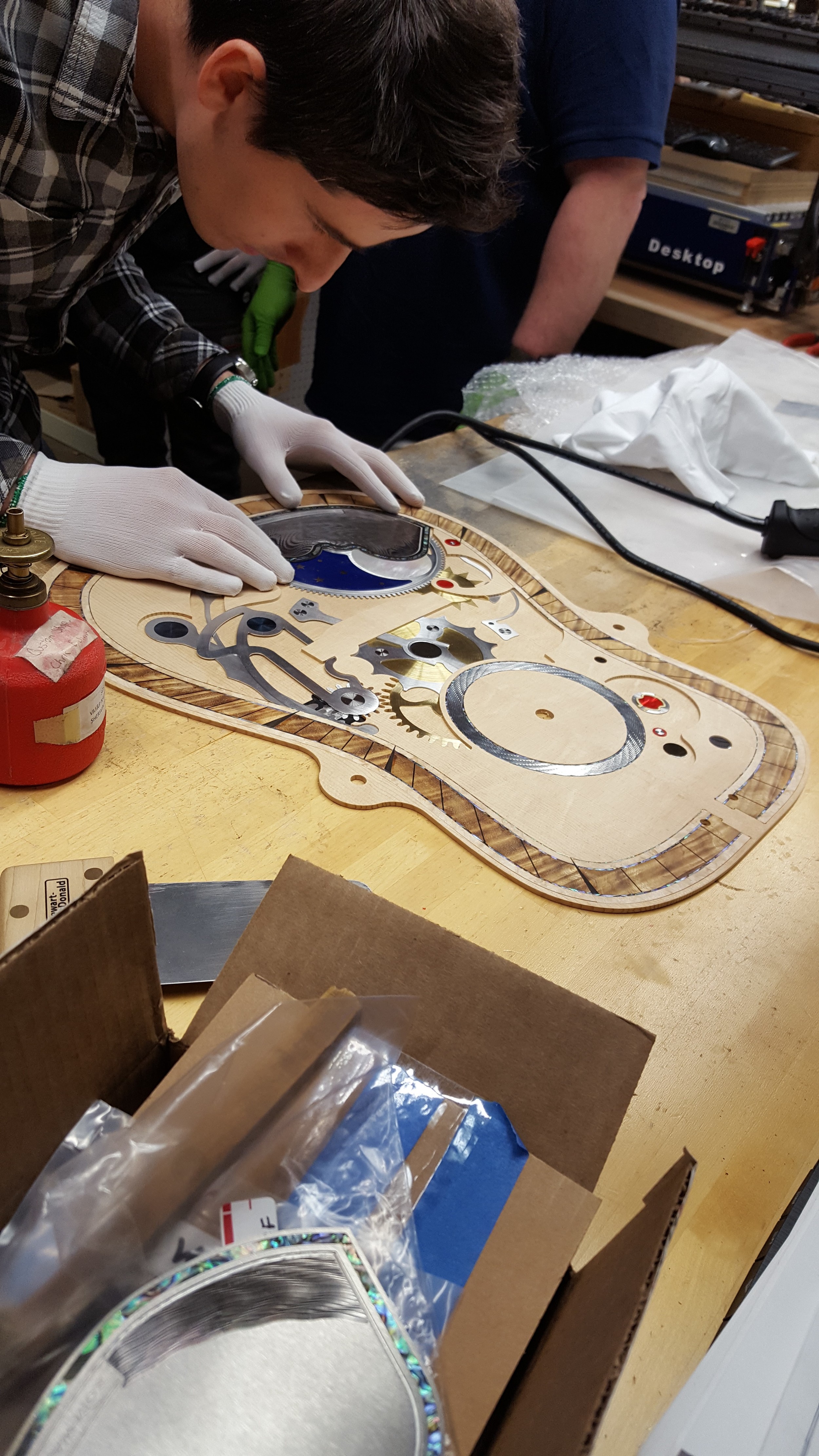
Preparing the Adirondack top to receive the master pieces for inlay. No going back from this step. . . it's on!
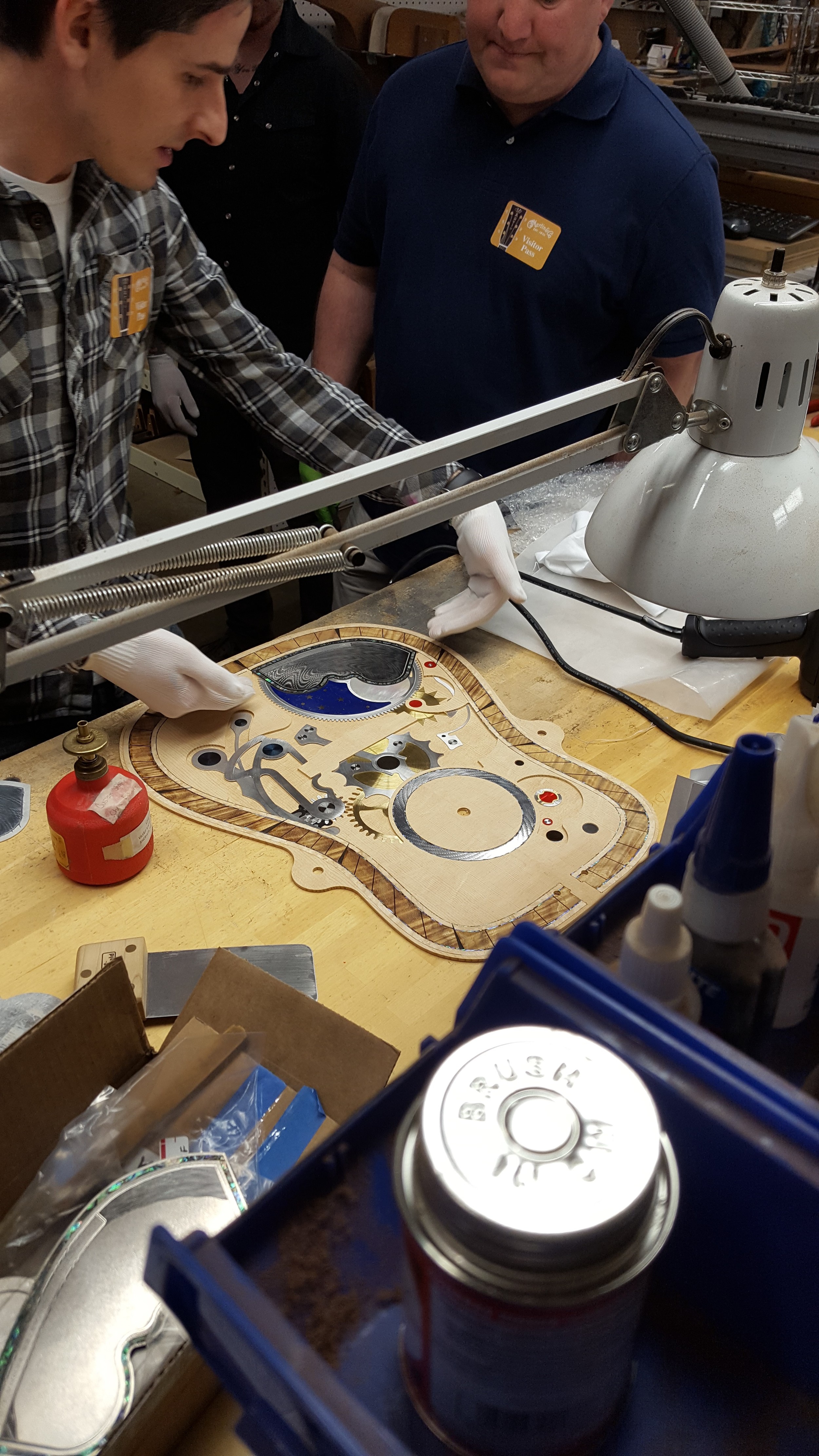
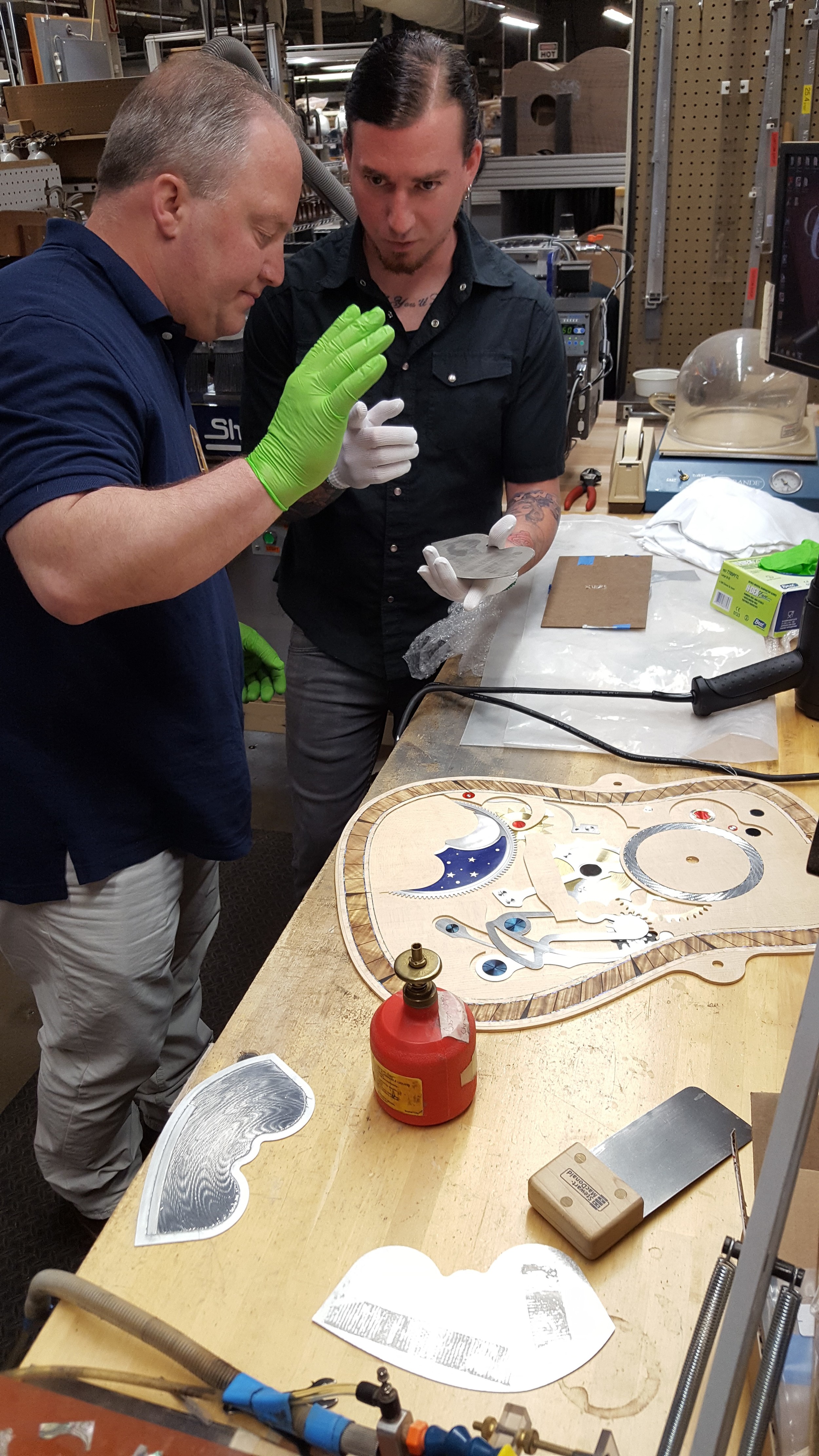
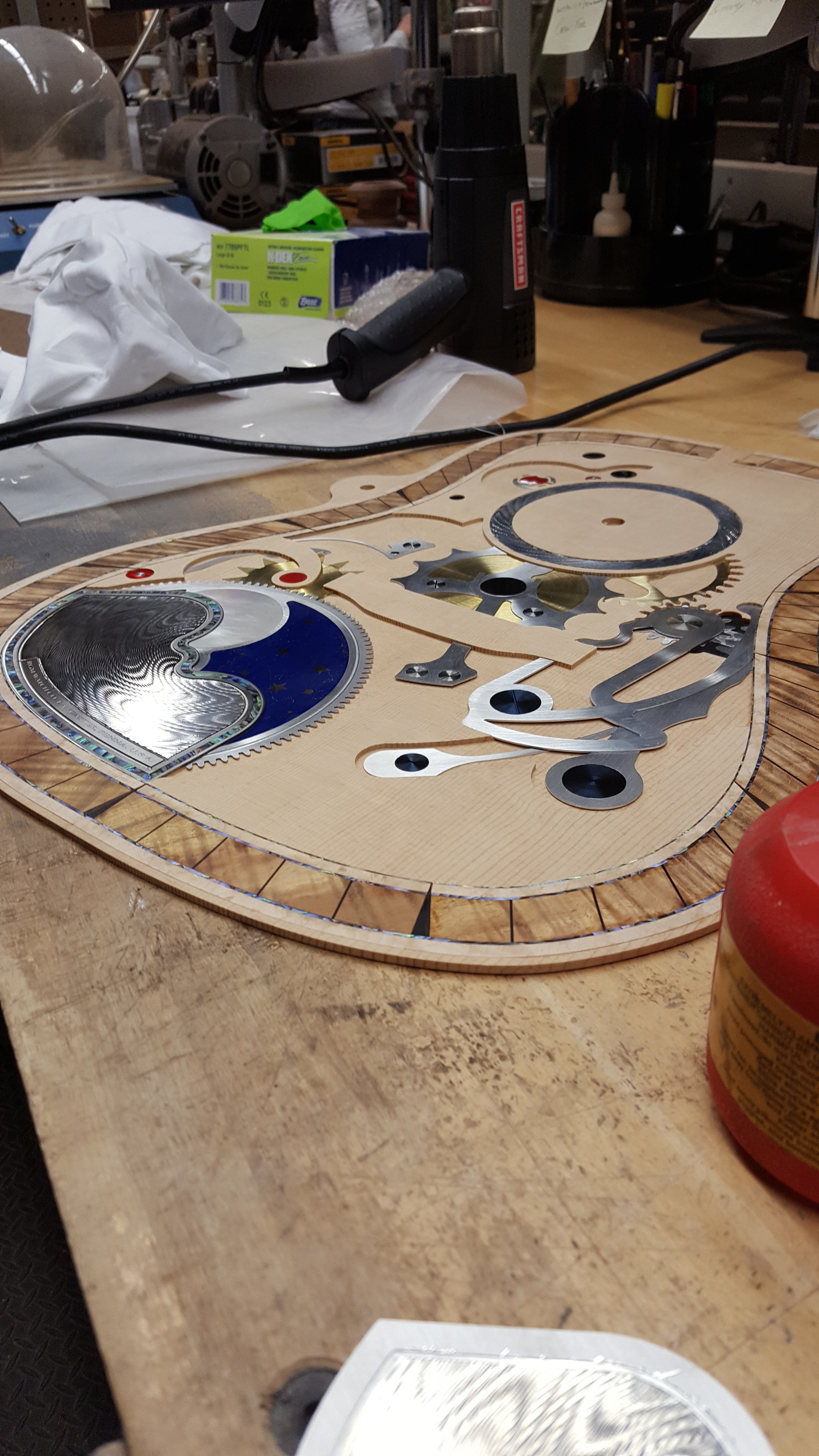
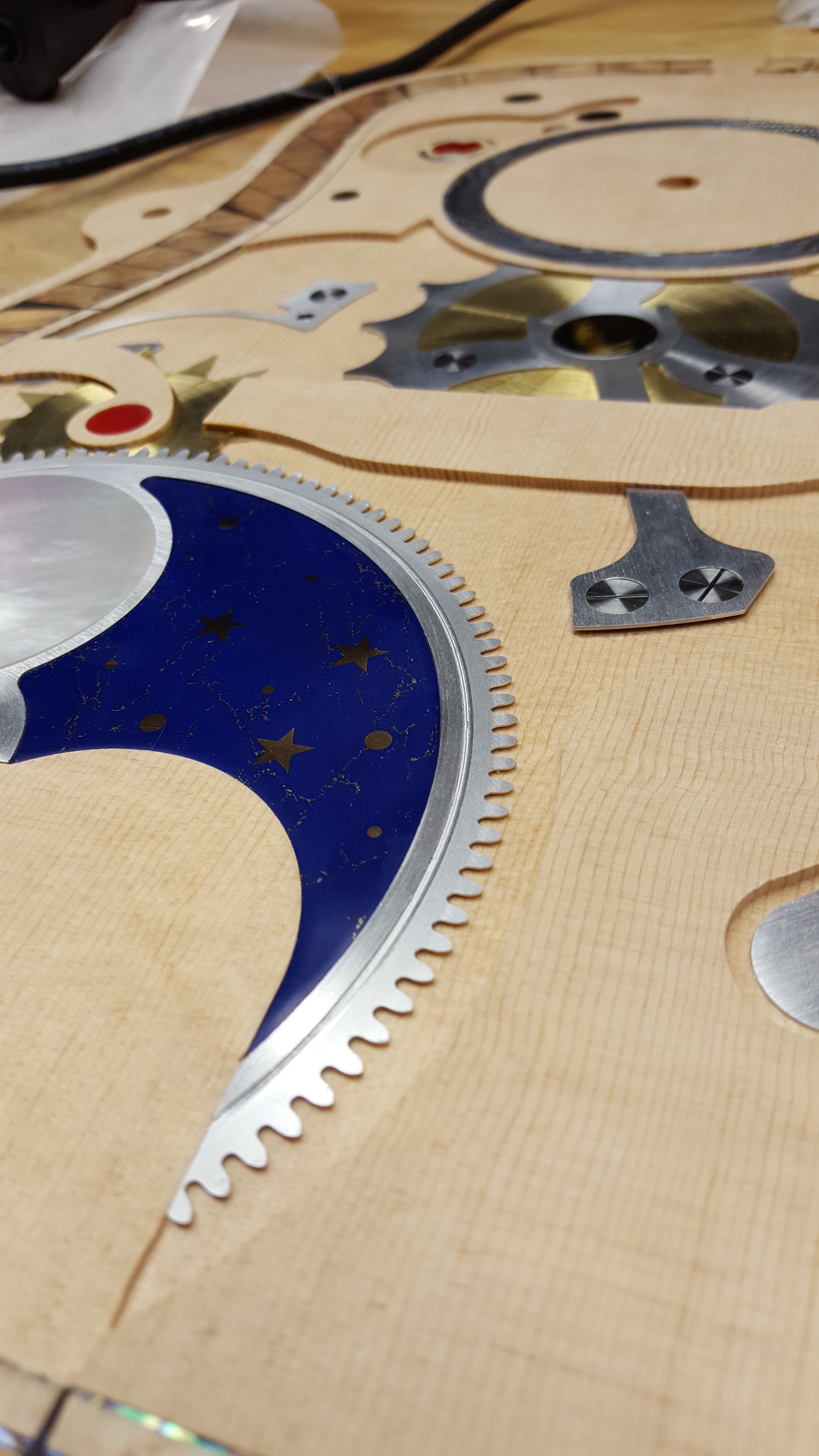
Close-up of the final placement - pre-embedding.
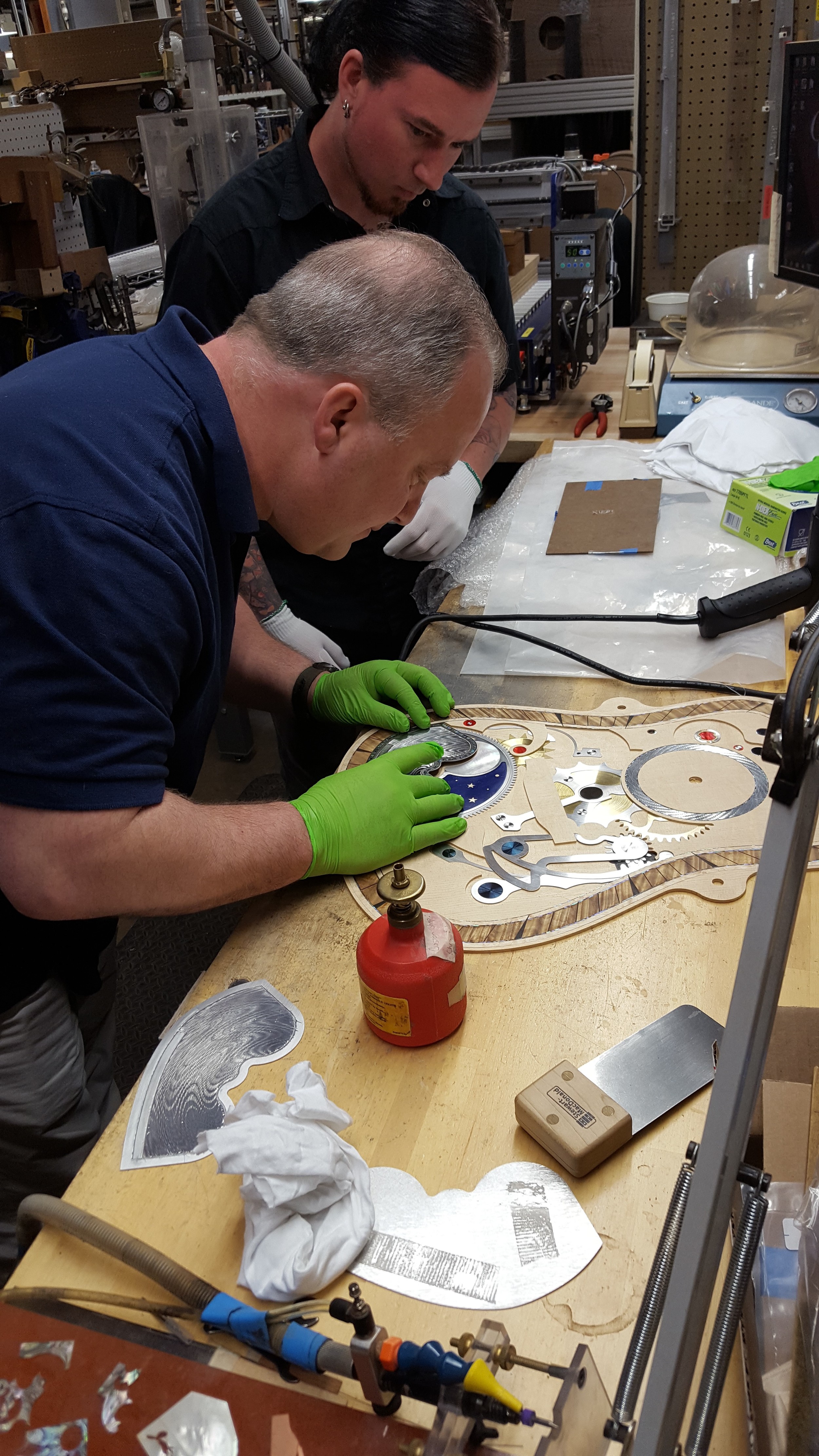
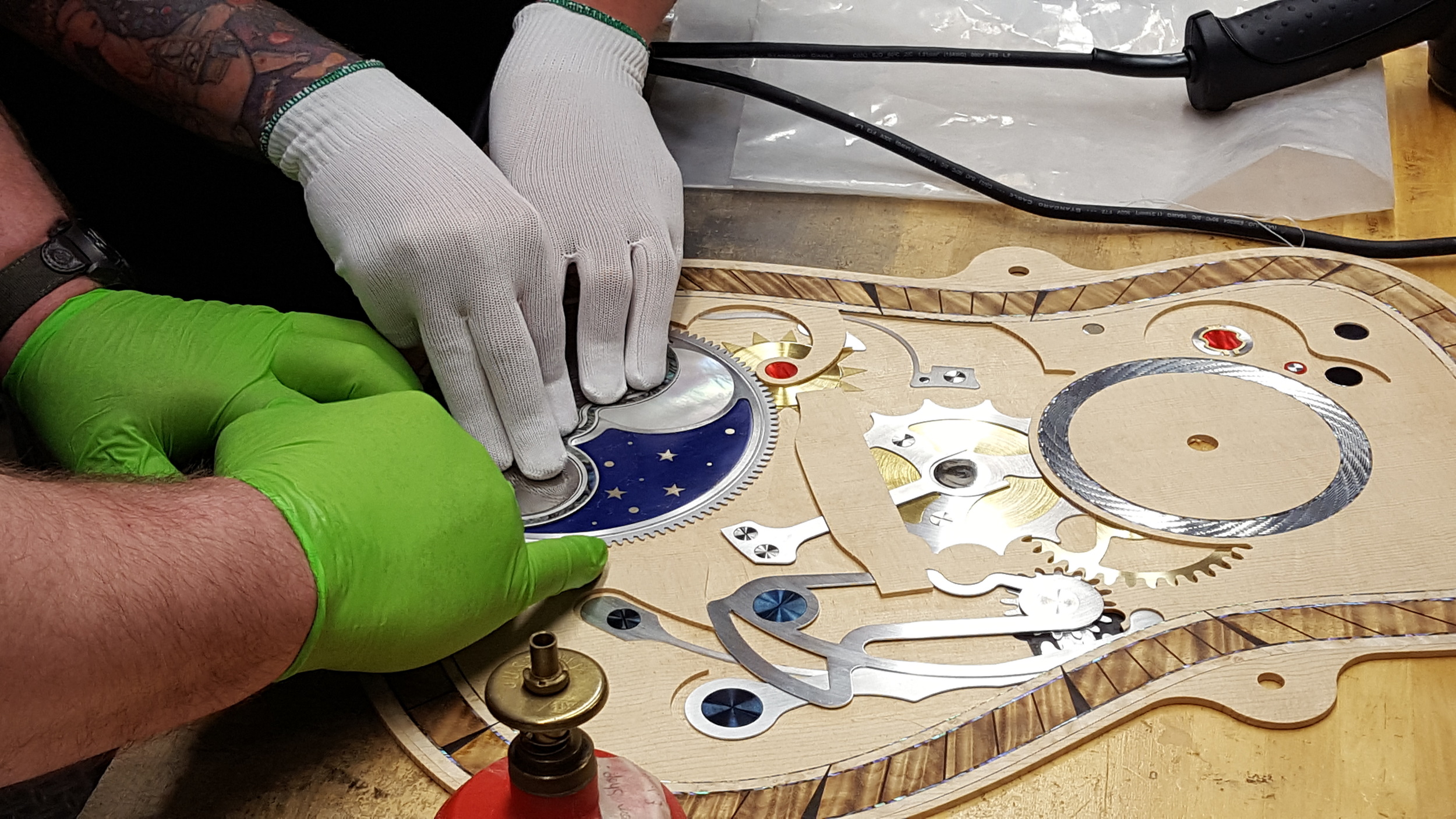
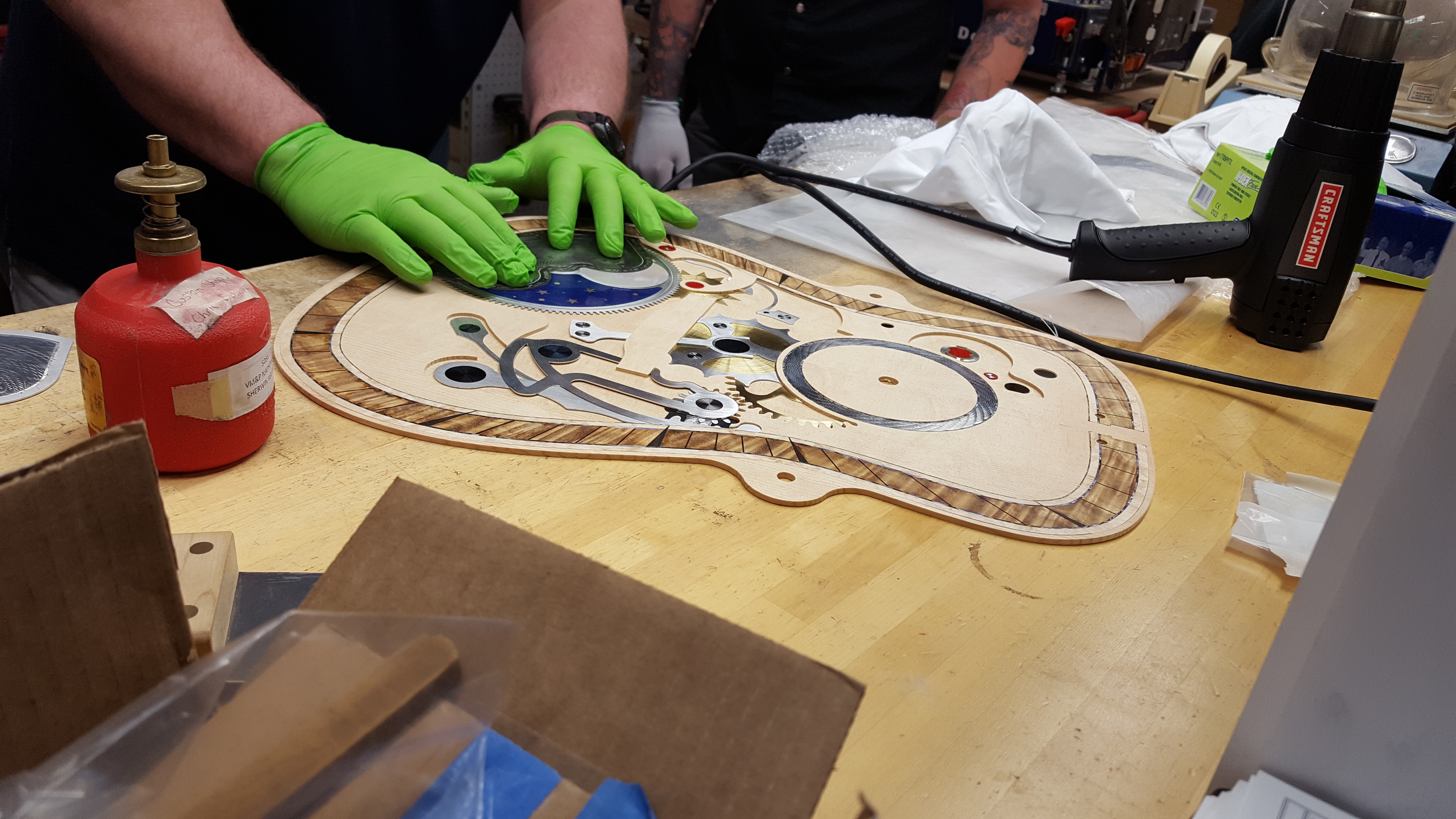
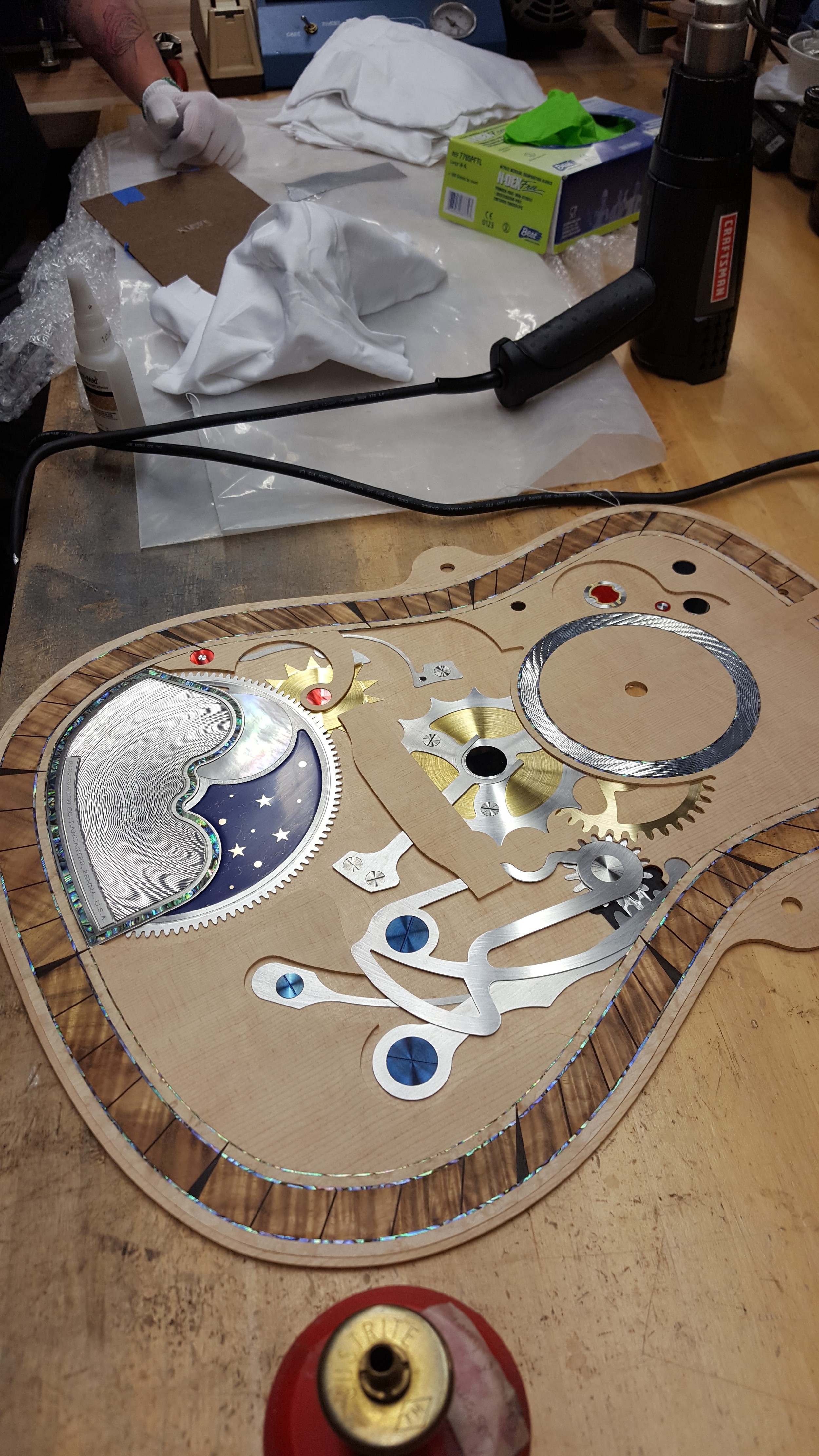
Top components in place & ready for placement of barrier prior to embedding.

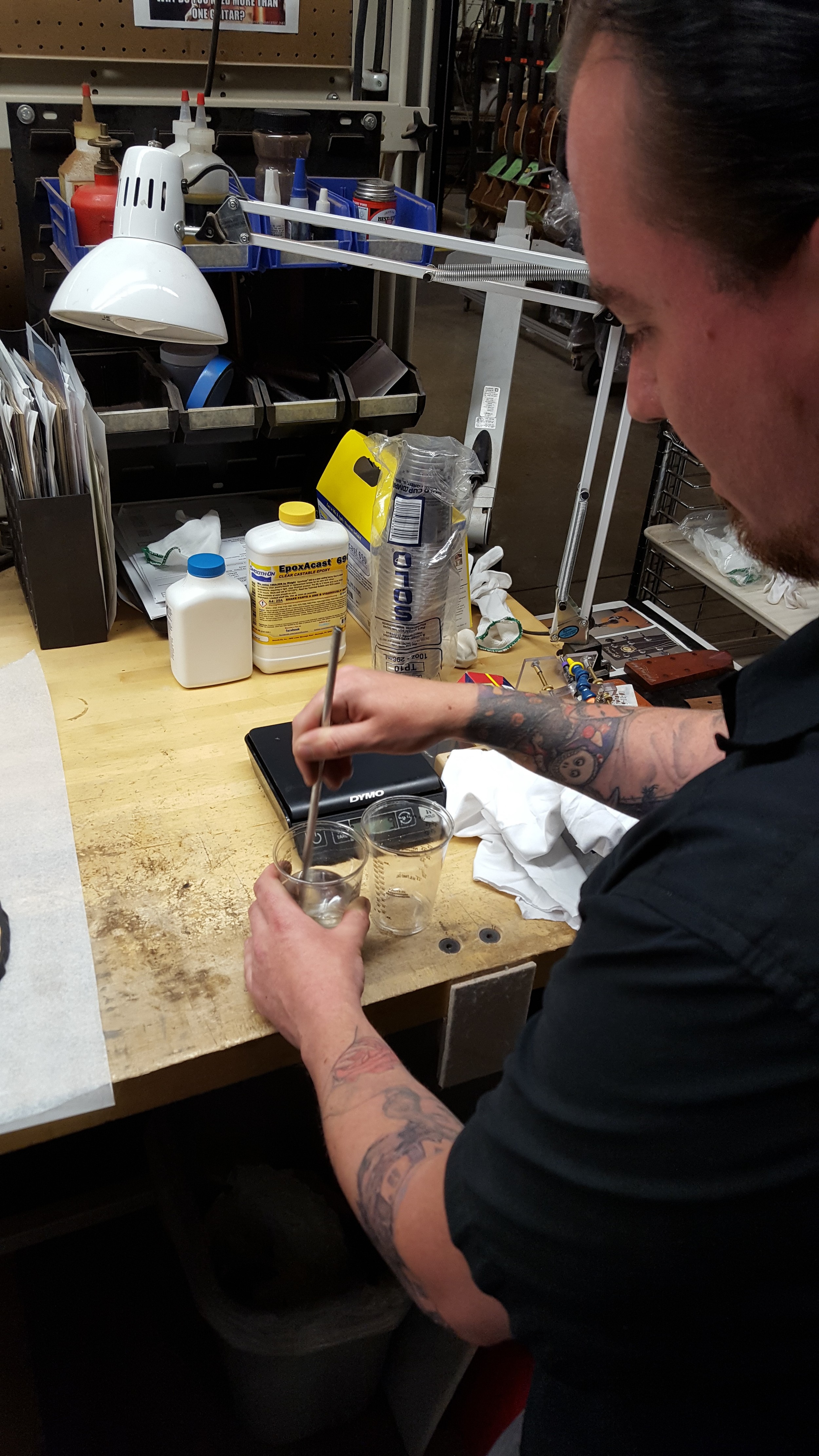
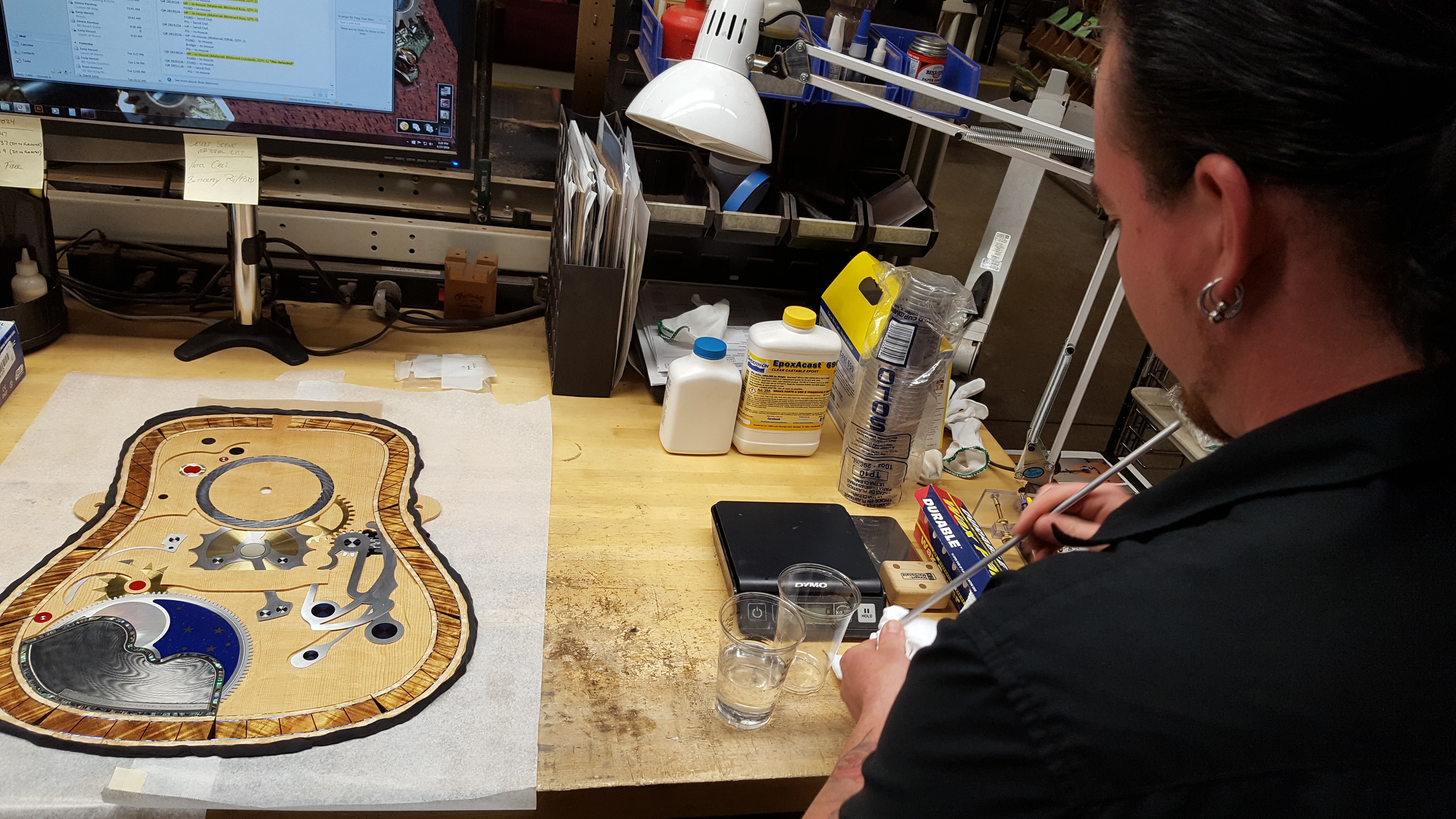
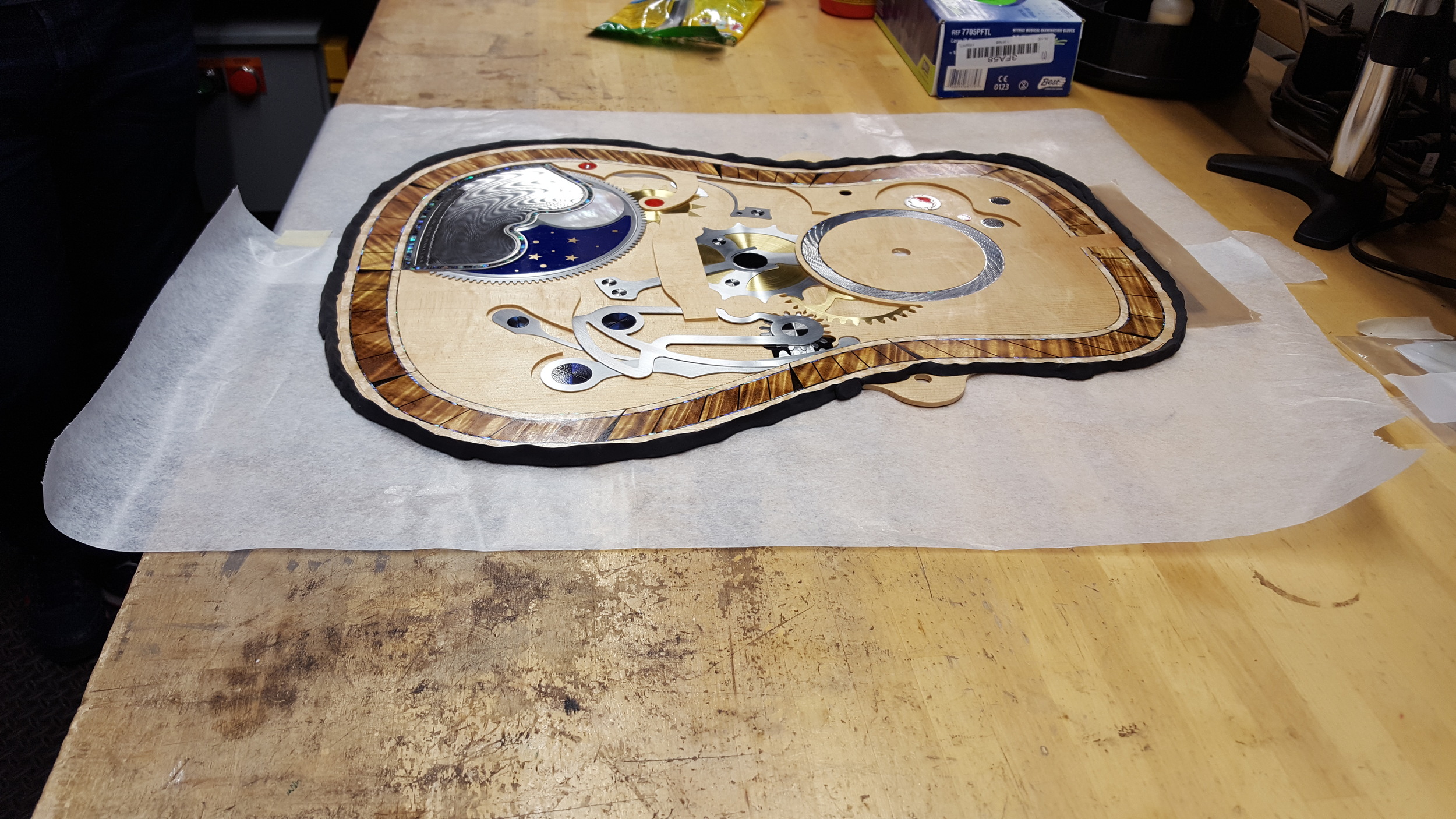
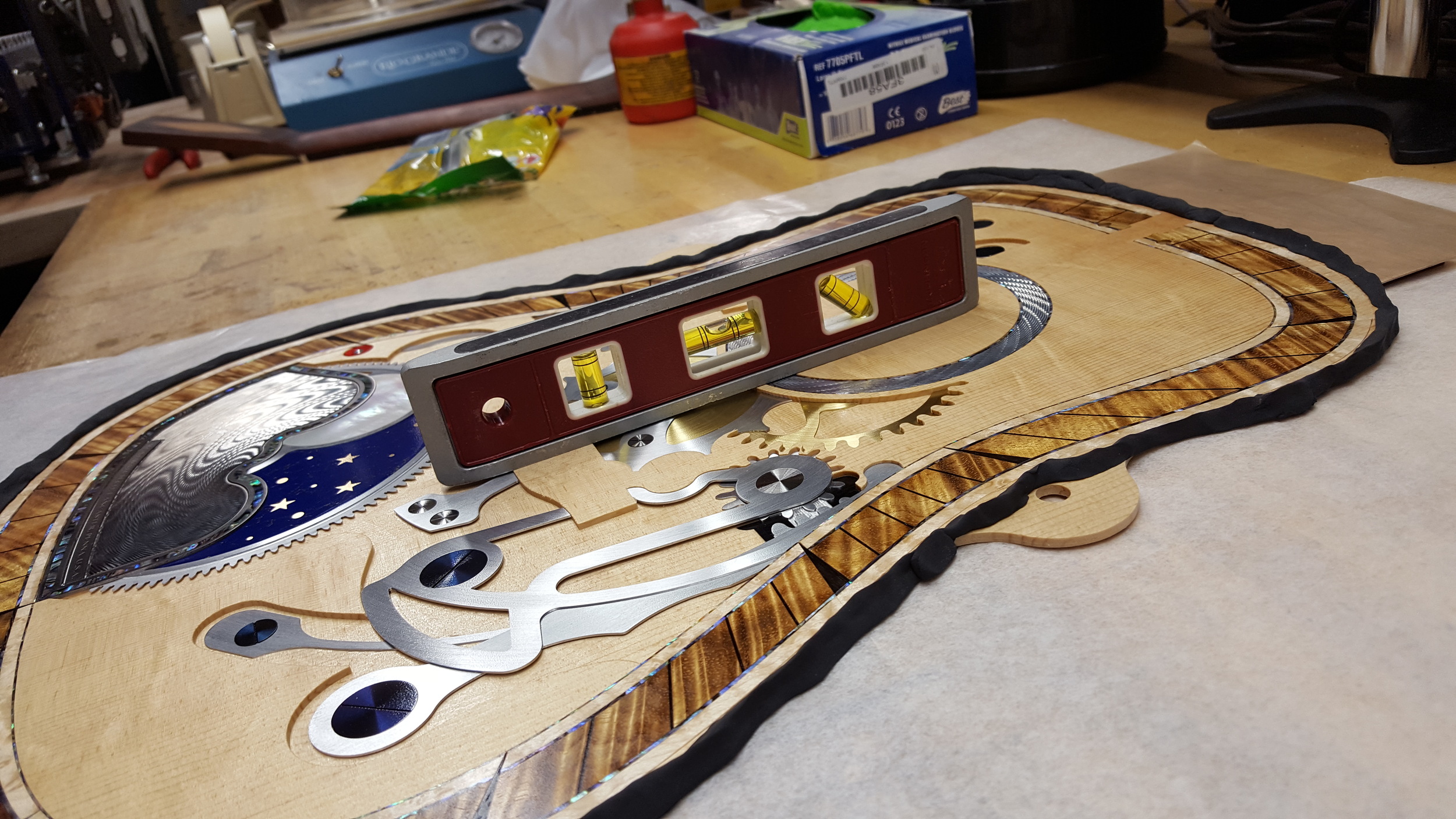
Checking for true-horizontal minutes before the point of no return.
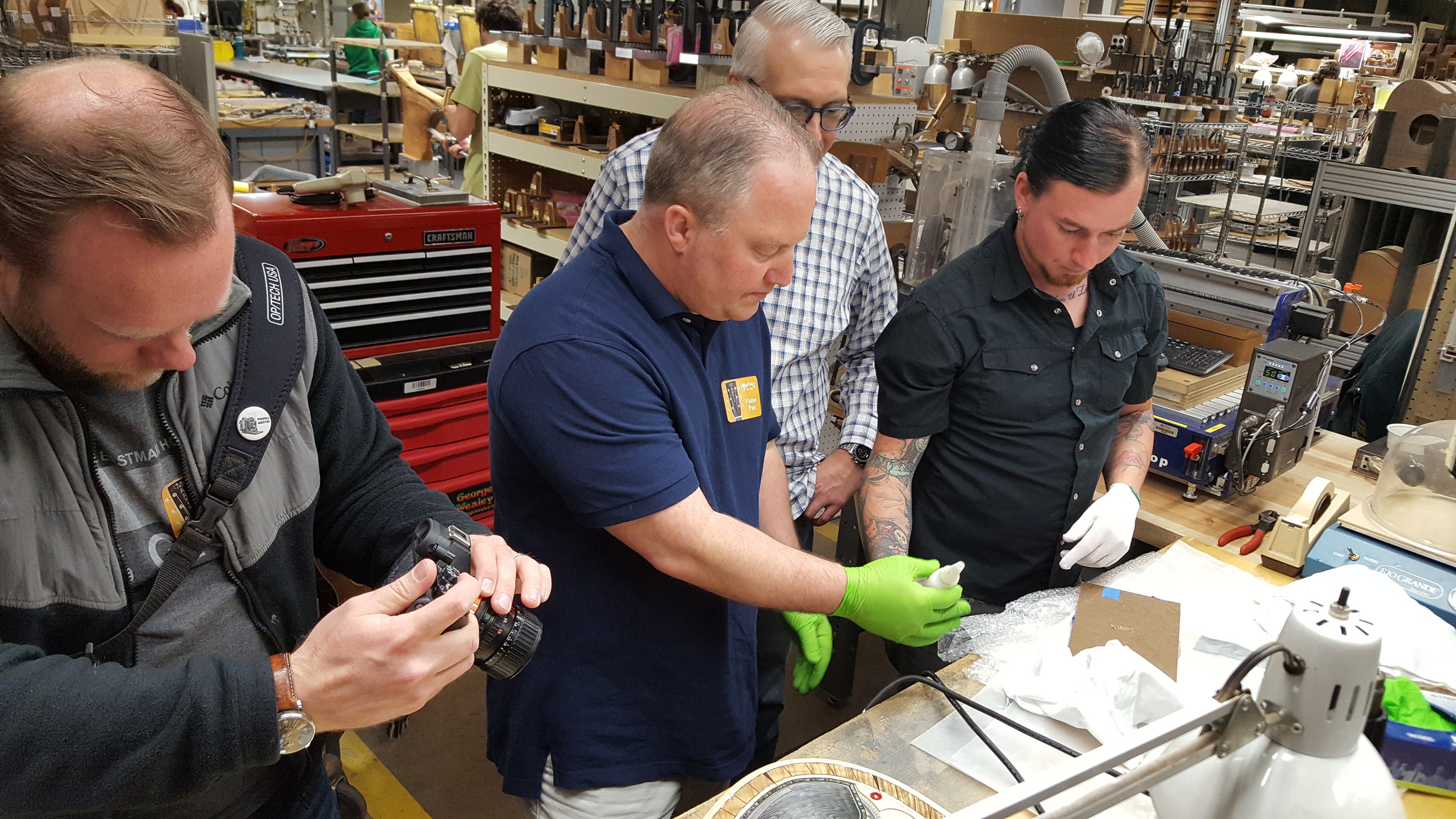
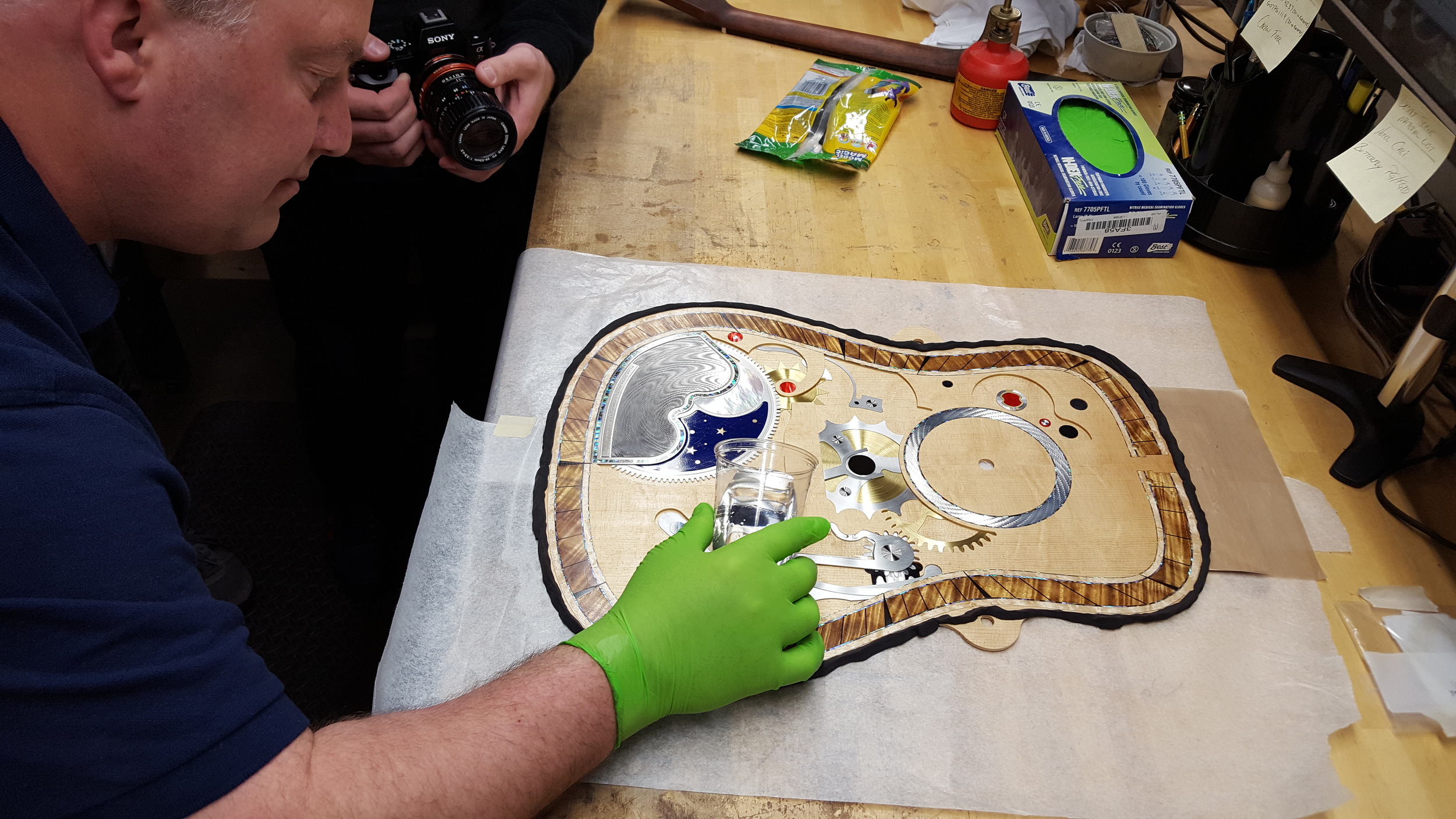
Beginning to flow construction resin across the top assembly. Steady hands required.

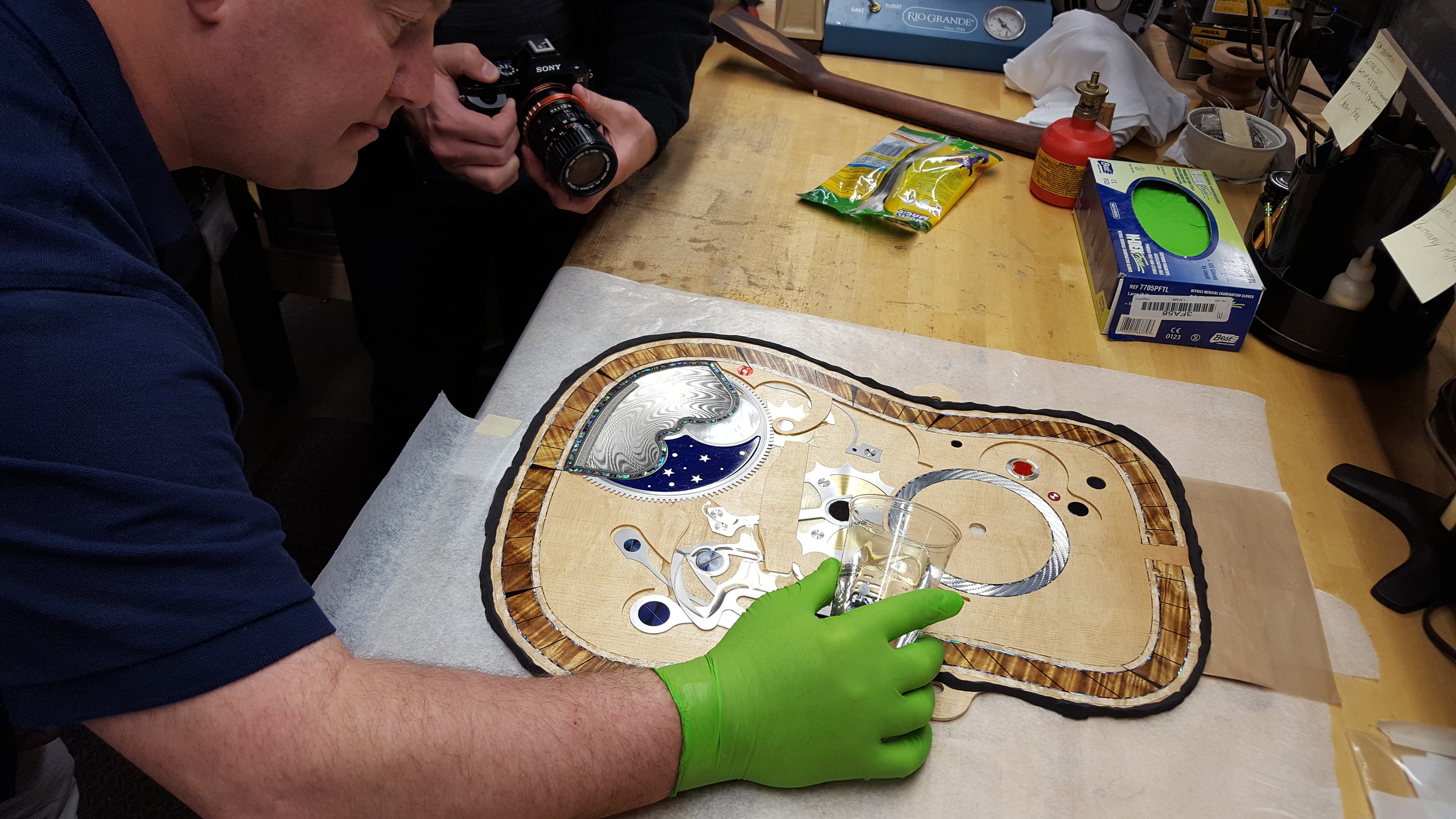

Members of the construction team.